New Wood Product Aims to Cut Building Emissions
Innovative technology offers a strong, lightweight alternative to steel
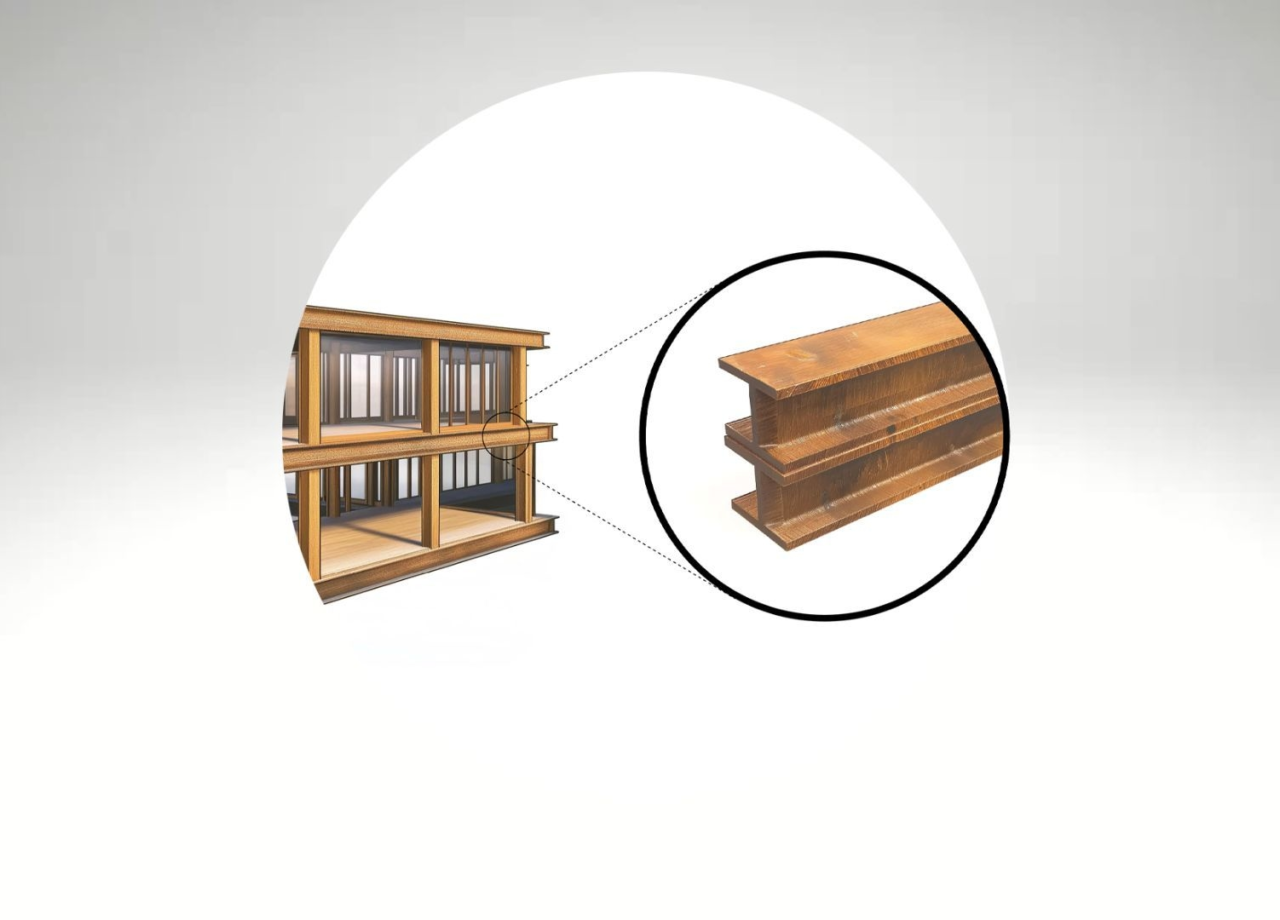
What is 50% stronger than construction-grade steel, six times lighter, and 100% biodegradable? The answer is wood, albeit with some processing required. A new technology to transform wood into a more effective construction material is heading to the commercial market as an alternative to carbon-intensive steel. As forest owners in the U.S. continue to face a fluctuating market, this innovation could eventually lead to a new source of demand.
The technology was developed by a research team led by Dr. Lianbing Hu at the University of Maryland. He founded the start-up company InventWood to take the product, called MettleWood, to the commercial market. They will soon open a pilot manufacturing facility in Frederick, MD, and expect to start production at 1 million square feet of MettleWood boards each year.
The U.S. Department of Energy sees MettleWood as a potential climate solution. In 2022, Hu’s lab received a $20 million grant through the Seeding Critical Advances for Leading Energy Technologies with Untapped Potential (SCALEUP) program. The program aims to support the scaling of high-risk and potentially disruptive new technologies in the transition to clean energy. Today, steel and concrete collectively account for about 20% of global emissions. According to InventWood, MettleWood could replace up to 80% of these two materials worldwide, reducing greenhouse gas emissions by over 2 gigatons.
It may also encourage healthy, diverse forests. MettleWood can be created from almost any wood, including the abundant, fast-growing, and even invasive species. This would provide foresters with a cost-effective way to clear invasive species and replace them with high-value or native trees. And, it is a technology that can be implemented worldwide.
To create MettleWood, InventWood cuts and trims the wood before processing it with heat and chemicals to break down and remove the wood’s lignin, the natural glue holding the cells together. The remaining cellulose, now a spongy structure, is compressed until the fibers are packed densely together. With a finishing polish and seal, and the result still looks like wood – because it is – but has improved characteristics. According to the company, the result is one-fifth the volume of the original wood but 20 times stronger. The process also makes MettleWood resistant to many of wood’s common threats, including moisture, fungus, termites, scratching, denting, and fire (it has achieved a Class A fire rating).
As with any new innovation, there are inevitable limitations. More research needs to be done to understand the carbon impact of MettleWood. The production can be costly or energy- and chemical-intensive, which may offset the environmental benefits. Even with an optimized process, production costs, efficiency, and other factors may limit scalability. Meanwhile, steel and concrete industries are simultaneously working to decarbonize their sector, potentially reducing the need for MettleWood.
Still, for the InventWood team and research teams worldwide, there is a hope that the same building material that humans have been using for millennia can be adapted to meet today’s growing needs.